Silestone used here as the countertop.
Photo courtesy of Silestone.
The use of quartz surfacing has grown over the last several years. It is becoming increasingly popular because of its durability, unlimited color options, consistency of the slabs, nonporous nature and ease of maintenance.
I had an opportunity to interview Edwardo Cosentino, the son of the owner who runs the American operation.
In 1978, Paco Cosentino took over his father’s modest stone business in Almeria, Spain, which at the time had 14 employees. In the late 80s, he envisioned transforming stone scrap into an entirely new surface for the marketplace, which would one day become Silestone. Cosentino launched Silestone in 1991, and expanded its business to the U.S. in 1998. Dekton, an ultra-compact surface, was launched to market in 2013. Today, Cosentino has a presence in 40 countries and almost 5,000 employees worldwide.
As the 38-year-old became the head of Cosentino’s North American operations, now based in Miami, FL, Eduardo has spearheaded the manufacturer’s growth in the U.S., which now makes up more than 60 percent of its global sales. Eduardo continues his father’s passion for innovation and commitment to keeping its people, whom they call “the Cosentino family,” first.
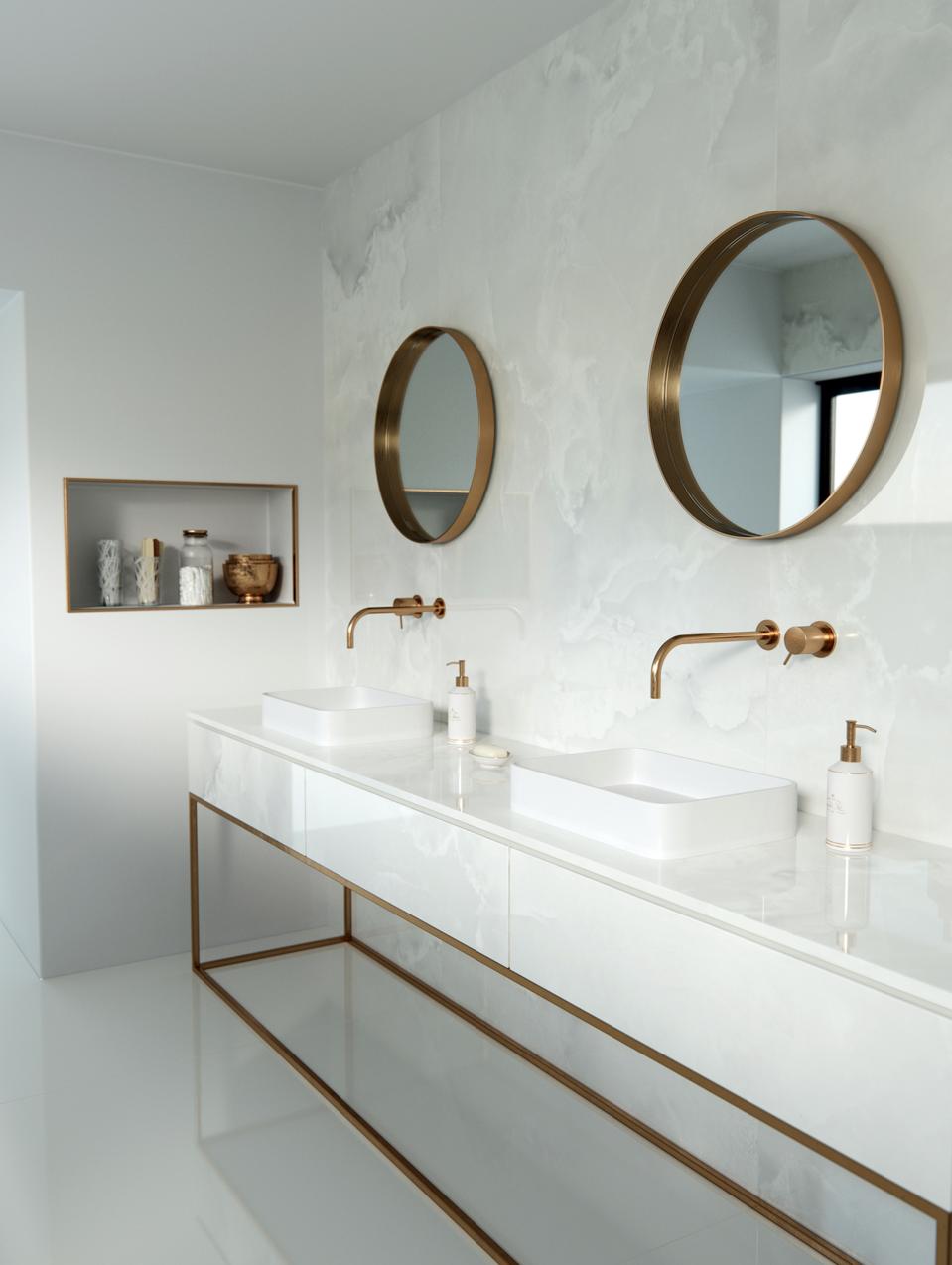
Dekton surfacing used in the bathroom .
Photo courtesy of Cosentino
How did your experience watching your father shape Cosentino’s culture, and you as a leader?
My father built Cosentino with a “people first” mentality, which is evident in everything we do. He taught me this is instrumental in not only making a business successful, but making it a great place to work. He taught me that our business is not just about words, ideas, or the end-result that drive the bottom line, but the qualities that live and breathe in our organization because of our people.
Did you always know you wanted to follow in your father’s footsteps and go into the company business?
Ever since I can remember, I’ve had the passion and desire to be a part of it. My fondest memories are tied to this business: Spending weekends with my father at the quarries in the Filabres mountains in our home country of Spain, or waking up before sunrise to visit the factory where the first Silestone slabs were produced when I was just 10 years old. The memories are endless.
Why do you think the demand for quartz surfacing has grown so rapidly in recent years?
The increasing demand for quartz is a direct result of our evolving world and lifestyle. People want quality and durability without compromising beauty, which is exactly what quartz provides. And as we’re all living, working and learning at home, wear and tear on our homes has never been higher, and homeowners are experiencing the importance of durability and ease of care now more than ever. Silestone captures the beauty, drama and soul of natural stone — but with a greater durability that doesn’t demand the hassle of sealing that marble and granite require, due to their porosity.
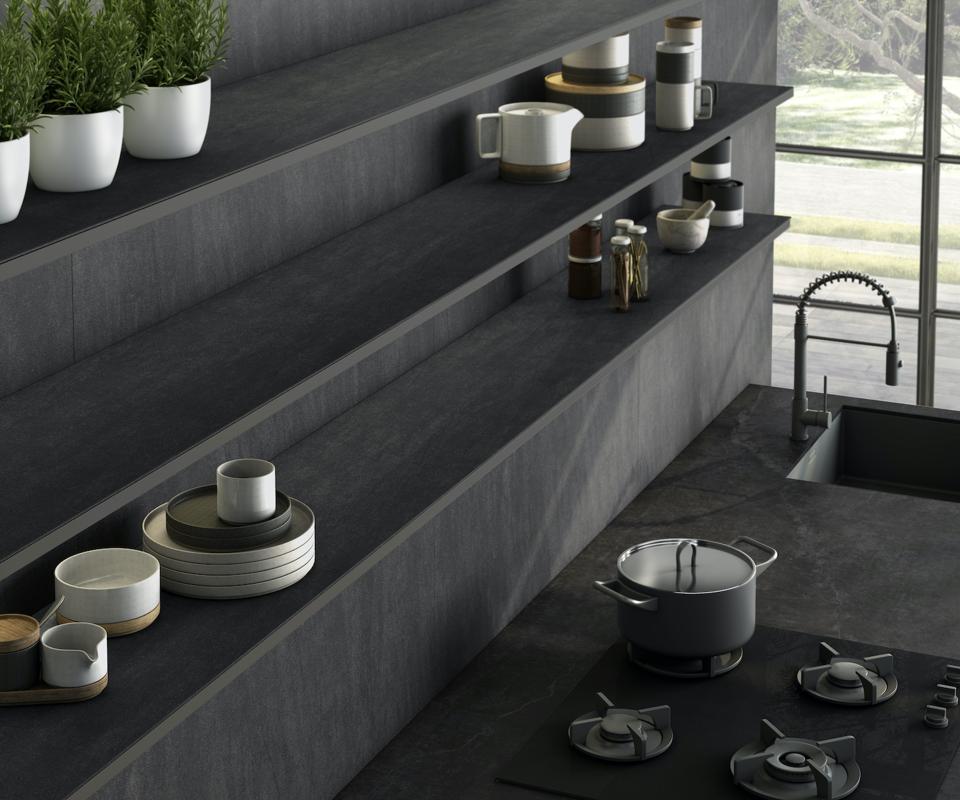
This is a slim Dekton surfacing used on the countertop and shelving
Photo courtesy of Dekton
What are the differences in the Silestone and Dekton companies?
Silestone and Dekton are two different materials manufactured by Cosentino. Both are unique in their characteristics, but created with the goal of imagining and anticipating our clients’ needs. Innovation is at the very core of Cosentino, and our brands are a direct result of deep market research and innovation.
Silestone® is composed of over 90 percent of incredibly hard and resilient raw materials, such as natural quartz and recycled glass. It first came to market in 1990, was introduced to the U.S. in 1998, and has led the industry ever since. Consumers have come to trust Silestone for its durability, design features, as well as its color consistency and expansive offering of colors and finishes.
Dekton® is our newest introduction — the first-to-market ultra-compact surface that we launched in 2013. In four hours, we mimic what takes Mother Nature millions of years to create. The result is the most durable surface on the market, created from a blend of raw materials used to manufacture glass, porcelain, and quartz. It’s favored not only because of its durability (zero porosity, high resistance to UV exposure, heat, scratches and stains) and zero maintenance, but its versatility of use, including countertops, flooring, wall cladding, and more — indoors and out.

Silestone surfacing used for the countertop in this kitchen.
Photo courtesy of Silestone
COVID had a tremendous impact on so many industries. How did it affect Cosentino?
The pandemic has impacted every industry and every organization; Cosentino was no different. And with our Silestone and Dekton manufacturing facilities based in Spain — a country hard hit by COVID — our top priority was to keep our employees, customers, and operations safe by increasing safety measures and adapting production accordingly.
As my father has taught me, the right mindset can use moments of hardship as fuel for innovation. And that’s exactly what we did. 2020 will prove to be another year of significant innovation for Cosentino that will propel the company and industry as a whole forward.
What are the latest innovations from Silestone?
We recently unveiled our new HybriQ+ technology, an industry-first production process and a new hybrid formulation of Silestone, comprised of minerals and reused raw materials, with a significant reduction in the use of quartz – all to promote greater safety in the production and fabrications sectors of the industry. This cutting-edge technology represents a qualitative leap in the evolution of Silestone in terms of functionality, quality, beauty, and sustainability. We also amped up our sustainability efforts and are proud to say that today our production processes run on 98 percent recycled water and 100 percent renewable energy, as well as reused raw materials.
Our latest series, Silestone Loft, which just launched this October, was inspired by some of the coolest urban neighborhoods in the world. There also continues to be a strong interest in industrial, cement-style colors, and we anticipate these five shades (Camden, Seaport, Corktown, Poblenou, and Nolita) will not only meet, but exceed demand and lead the industry trend.
What are the latest innovations from Dekton?
Dekton Slim has truly been a game-changer for the industry. At only 4 mm thick, it’s half the thickness of the thinnest Dekton slab! It offers all the technical and mechanical features of traditional Dekton, but in a thinner, lighter, and more manageable format for installation. This means we can now offer solutions for even more projects that require high-performing, lightweight materials, such as furniture, cabinetry, backsplashes, wall cladding, and more.