Offsite manufacturer Veev is incorporating technology into every aspect of the process and trying to … [+]
Veev
There are hundreds of different products that go into the construction of any one home – a number that no housing data team is tracking or can nail down.
Yet, the number is increasing exponentially as more and more technology is created to entertain, to improve efficiency, to maintain wellbeing, to facilitate comfort and to be more resilient. While adding the products may improve the resident experience, at the same time, it complicates the design, tangles the supply chain and adds cost.
The Time Equation: Simplifying the Supply Chain
One of the biggest benefits of prefabrication is reducing time. In 2018, the US Census Bureau stated that the average length of time to build a conventional, onsite single-family home, from permit to move in, was seven months.
In offsite home construction, that can be reduced to just days or weeks. And, that’s traditional offsite construction, the type that is using the same materials and same processes as on site.
Amit Haller is founder, chairman and CEO at Veev a California-based manufacturer that mixes a variety of disciplines to explore real estate challenges and approach them with a more modern fix, including changing the materials.
For example, Haller looked at the walls and the traditional way that they are put together on site—drywall that is easy for a contractor to install. But, drywall has taping, mudding, painting, painting again, baseboard and trim, which not only add up to a lot more time, but a lot of cost. While purchasing a sheet of drywall may only be $1 per square foot, the cost starts to double or triple after all the extra work is done.
Veev chose a new wall material, LG HI-MACS, an acrylic solid surface. As Haller describes it, “It’s magic in the CNC machines, very precise.”
Plus, it’s painted and prefinished. Although the material is more expensive, Veev calculates the end cost is half of traditional drywall installation. There are other advantages as well. It’s antibacterial, it doesn’t stain, it is non-scratchable, and it will not mold. Haller looks at it like the superman of materials, for half the cost.
The Veev machines cut the material exactly to the wall specifications, cutting out space for a door and other openings. With the acrylic solid surface, the material that is cut out can then be used to make the door, minimizing waste.
“The door is incredible because it is the same material, it’s heavy,” said Haller. “That’s the type of thinking that we deploy in everything we do.”
Then comes the really interesting part. The walls are finished with a 3D printer, that simplifies the supply chain at the same time that it allows for major customization. The 3D printer can print any texture or color, even to look and feel like wood or print in a picture of a child’s favorite character.
In the same way that they recast walls, the Veev team is rethinking tiles, windows, exterior cladding, HVAC system and all other aspects of the home with a very multidisciplinary team from scientists to software engineers. Haller says the goal is to be four times faster at half the cost without compromising quality.
Baya Build is another offsite manufacturer based in Indiana, founded by James Casper, that is simplifying the supply chain.
“We have a very smart design, 10.5” wall with cavities to reduce energy consumption with high R value, to category 5 strength and to California seismic requirements,” said Casper. “We prefabricate every component ahead of time in the factory and we’ve labeled and organized it all in a 40’ container. So, the whole process can eliminate 80 to 90% of the various tradespeople. No mudding, taping, foundation.”
Duncan Mayes, renewable, sustainable materials innovation expert and consultant, points out that Stora Enso, a renewable materials company, is integrating RFID technology on their manufactured wood solutions to facilitate installation. By looking at the design on a device on site, the crew can see the whole building structure constructed in a BIM system as a digital twin, and identify where an individual piece goes by scanning the RFID code.
Finding Value
Zenon Radewych serves as a principal at WZMH Architects, a Toronto-based global architecture firm, and is realistic about the value of prefabrication.
“You have to bring other value add because prefab isn’t necessarily cheaper,” says Radewych. “Technology is a wow factor and prefab is a wow factor. When you combine them both, that’s when you see the true value add. That’s the real trick – who knows how to combine both.”
In partnership with Stephenson Engineering, his team at WZMH is using the advantages of technology to enhance the products and materials that are being installed in the home. They have built a prototype of a floor system that uses plywood sheets that are sized for the sub-floor, joists and the ceiling membrane, all cut and assembled in an automated and prefabricated process.
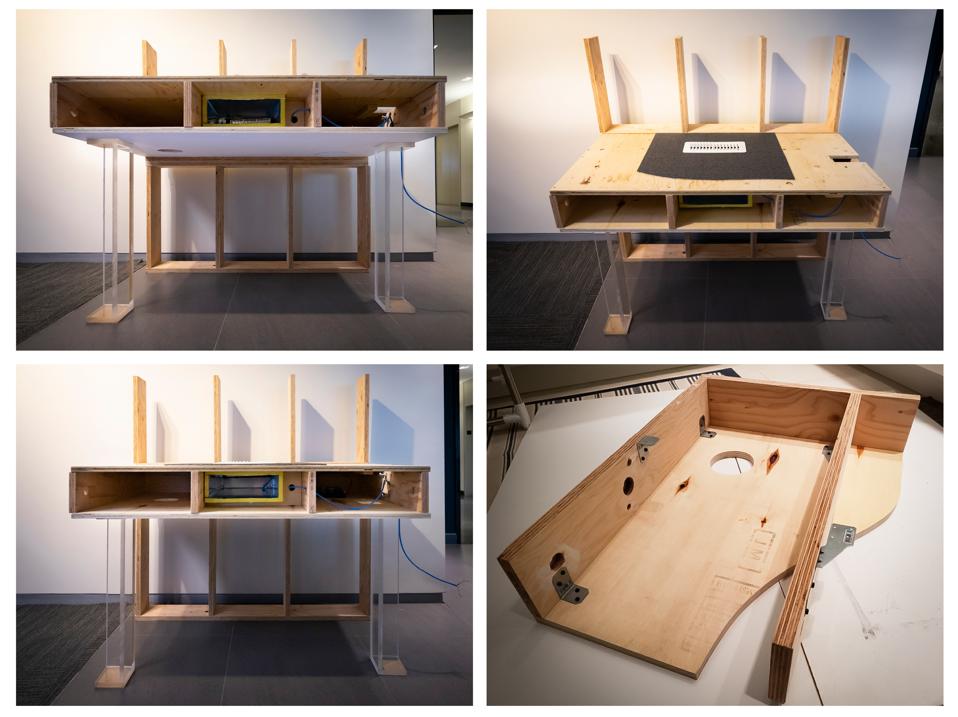
Intelligent stressed skin panel
WZMH and Stephenson Engineering
When compared to conventional lumber, the complete plywood solution provides additional strength, longer spans, and creates a relatively thin sandwich that is used for wiring, duct work, lighting and all other home components such as security and audio-visual systems.
Jason LaFleur, senior program manager at GTI Energy, an advisory group addressing challenges in the energy value chain, is looking at how technologies can be integrated together and deliver optimal design and cost savings with housing manufacturers.
“The process of going through a modular manufacturing environment forces a lot of attention and thought that otherwise might not occur with onsite construction because you have to be more intentional with the sequencing of various aspects of construction,” LaFleur said.
The research group is currently working with Dvele, a California-based home manufacturer, to bring vacuum insulated panels into the market. The collaboration sees the advantage of the manufacturing environment where there is more control and less propensity for errors with vacuum insulated panels. The vacuum needs to stay intact so the careful process of the manufacturing floor is critical. Plus, it has to be aligned to maximize the structural integrity and minimize the thermal bridging. All the risks are decreased or minimized with a careful, high quality offsite assembly.
“Vacuum insulated panels perform 20 times more effectively than what is onsite,” said LaFleur. “You get the same benefit in one inch what might take six to seven inches of standard insulation material.”
Alison Donovan is senior consultant at VEIC and is working with modular companies across the country to model and analyze energy performance to advise on new and different ways to improve the energy efficiency.
“We really see a way to engage offsite construction in a way to make it more efficient,” Donovan said. “What we found and what we hope is true is a future to align efficiency, reduce costs, and increased quality from factory-built construction as the homes get more complicated, with grid interactions, resiliency measures, batteries, and solar storage.”
Ultimately the goal is to help reduce the cost for home owners, which VEIC thinks it can achieve at scale with prefabrication. A VEIC impact study of 97 zero energy modular homes showed $1.2 million in energy costs avoided and 2,313 metric tons of carbon emissions avoided during a period of six years ending in December 2019.
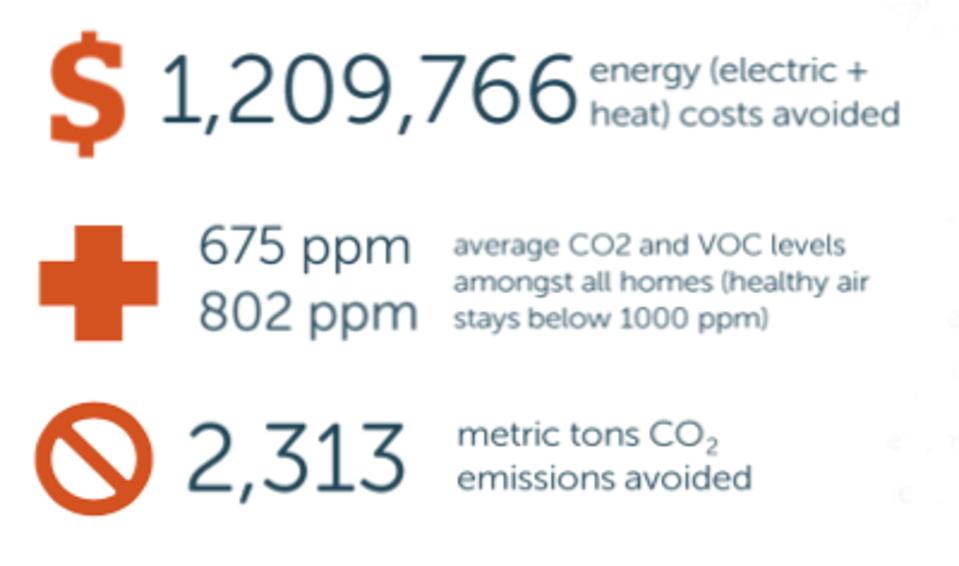
The Zero Energy Modular initiative results from 2013 to December 2019.
Efficiency Vermont
“The first cost may not be lower, but at scale there is the potential to be able to achieve zero net energy at no incremental cost,” said Donovan. “Just thinking about the building, maybe a zero-energy home has a $10,000 incremental cost. We want to make sure that home’s energy savings will pay off over the life cycle of the home and from day one when someone moves in the home, they save energy or get net metering credits. The threshold is you have to have a utility that has a net metering structure and not all utilities do.”
Technology at the Root
Then, there are the builders who started with technology as the basis.
“We think about Dvele more as a computer chip,” said Kurt Goodjohn, co-founder and CEO of Dvele. “What we found in research on the home buying experience is that they are excited when they buy the home, they are excited when it starts being built, and then they are excited when they move in. Then it fades. We want to offer home as a service.”
Dvele is extending the relationship with the buyer instead of walking away after purchase. With data security in mind, the client can elect to give Dvele access to help and provide services. The company has developed homes that feature sensors to provide predictive maintenance services, such as detecting air leakage, the supply of fresh air, and moisture, which Goodjohn likens to your car’s “check engine” light.
But, it takes the sophistication of the design and manufacturing environment to create that learning ecosystem.
“We didn’t ever intend to just be a builder of homes,” Goodjohn said. “We haven’t perfected manufacturing yet, but we get a hell of a lot better every day. With our next capital raise we want to automate the factory more. We do it all in parametric modeling and we spend a lot in getting all the homes fully digitized.”
Goodjohn is modeling the homes like software so that some things can be swapped in and out and if there is an upgrade in a couple years, the system is flexible enough to quickly and easily make the change. As another value add, the Dvele homes are 100% electric, can be off grid and the company is researching power storage for the homes.
Haller is thinking about Veev in a similar way by standardizing a wall system so that it can be plug and play, resembling what other industries have done, like cars, semiconductors or phones. The Veev system is light gauge steel that is fully insulated, zero waste and fully recyclable. All walls have radiant heating and cooling so the entire wall is a heating and cooling device. Plus, the walls themselves are all load bearing, so can be used to build up to eight stories in any shape or style.
Meeting Demand
“The major issue in the whole of Europe is that there is a shortage of millions of affordable homes,” said Dirk Arnauts, managing director, Zero Ready, a panel system for better energy performance. “If every able body were to start building, it would still take 216 years to make what is needed. You don’t just need to automate in a time like this, you also need to innovate. You shouldn’t automate an outdated system.”
Arnauts wants to move to the states and envisions creating a factory process like Tesla, using materials sparingly and combining more building methods into one process. He’s focused on simplifying the process with automation in the factory and during the design phase.
“It’s a very efficient way to work,” said Arnauts. “You don’t need to pull endless meetings. Everyone can work in the cloud base in the initial CAD drawings from the architect. Everyone can add their own bit and walk through it and see it in 3D. The program will not allow you to complete a wall corner detail if there is a clash. If you are working in a CAD environment, you can import the designs into a program and then have another program do the virtual reality possibility.”
Galiano Tiramani is the business development manager at Boxabl, a Las Vegas-based housing manufacturer that wants to go big, manufacturing at a higher volume to lower the cost of homeownership for everyone. The company is mass producing everything, processed by efficient, computer encoded equipment with bigger components for less labor.
Tiramani said they are looking at different building materials like steel skin and magnesium oxide board on the exterior, but the real magic is in reducing the number of options to mass produce. Boxabl offers just four kitchen layouts and four bathrooms, which all fit into a carefully vetted shipping and logistics process.
Click. Click. Home Owner.
Baya Build, Bloxabl, Dvele and others are in the process of online tools that take a matter of minutes to create a home, with a real time budget and bill of materials. The online order system would tie into the factory’s purchasing system, sending POs to vendors and then feed the design into the factory to start the manufacturing process.
During the manufacturing, site partners are notified and automatically scheduled to be there when the materials arrive.
Future Forward
The technology continues to evolve. GTI is developing next generation technologies to reduce energy loads—like mechanical systems, energy conversion systems, and low carbon fuels—that have been talked about for years but not in the market yet.
Mayes is also working on some cutting-edge materials, that are being developed to add more efficiency and lower cost. For instance, an Australian Finnish company he works with has is developing graphene to be used on large surface areas for leak detection now, and to eventually move beyond moisture sensing to indoor air and temperature control and in age care facilities to monitor falls. This highly conductive, single atom graphene layer is very thin and durable so can be used as a sensor very easily. Mayes and the team hope it will be commercialized in the next year.